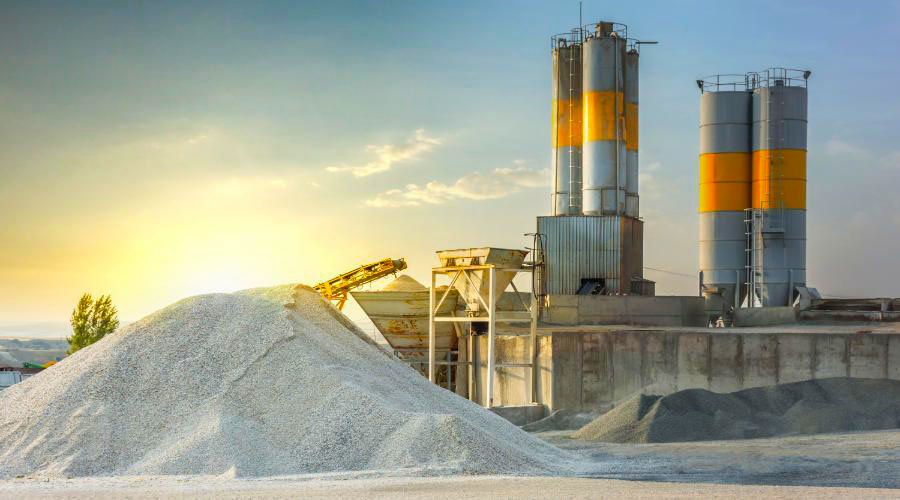
Crusher Wear Parts For Cement Industry
In the cement industry, crushers are critical equipment for processing raw materials like limestone, clay, and gypsum. These materials are extremely abrasive and cause rapid wear on crushing machinery. High-quality crusher wear parts for cement industry are essential for maintaining production efficiency, reducing downtime, and minimizing maintenance costs.
At Eone Wear, we specialize in manufacturing and supplying cement crusher wear parts that meet the rigorous demands of cement plants worldwide. Our wear parts are compatible with jaw crushers, impact crushers, hammer crushers, and roll crushers used in cement production lines.
1. Why Wear Parts Are Critical in Cement Crushing
1.1 Highly Abrasive Raw Materials
Cement production involves crushing limestone, shale, marl, and other abrasive materials. These cause severe wear and tear on crusher components. The continuous nature of cement manufacturing makes the performance and longevity of crusher wear parts even more critical.
1.2 24/7 Operation and Downtime Losses
Cement plants operate around the clock. Any unplanned shutdown due to worn-out parts can halt production, leading to significant financial losses. Regular inspection and proactive replacement of cement crusher parts help maintain consistent operations.
1.3 Need for Long-Lasting Components
Durable and reliable cement crusher parts help reduce replacement frequency, enhance equipment uptime, and improve overall plant productivity. Long-lasting components also minimize the risk of damage to adjacent machinery and reduce labor costs for frequent replacements.
1.4 Optimizing Total Cost of Ownership
Selecting high-performance materials for crusher wear parts reduces the total cost of ownership by improving wear life and reducing replacement cycles. Our team helps customers calculate lifecycle cost savings and ROI.
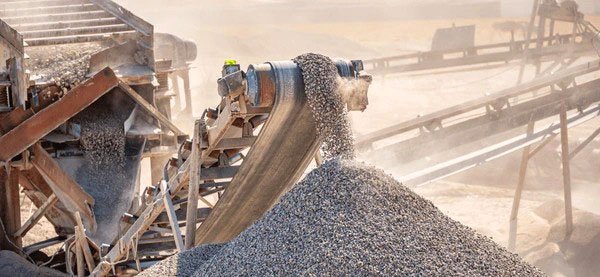
2. Common Crusher Types Used in Cement Plants
We supply wear-resistant parts for the following crushers commonly used in cement production. Each crusher type has unique operating principles and wear challenges.
2.1 Jaw Crushers
Jaw plates
Cheek plates
Toggle plates
Jaw crushers are primarily used in the first crushing stage. Our high manganese steel and TIC insert jaw plates offer excellent impact resistance and wear life.
2.2 Impact Crushers
Blow bars
Impact plates
Side liners
Impact crushers are used in secondary crushing and require materials like high chrome and martensitic steel for better wear and fracture resistance.
2.3 Hammer Crushers
Hammer heads
Grate bars
Breaker plates
Hammer crushers are commonly used for clinker and limestone crushing. We provide bimetallic and alloy hammer heads tailored for different raw materials.
2.4 Roll Crushers
Crushing segments
Tooth plates
Side combs
Roll crushers offer consistent product size control. Our wear parts are designed to maintain uniform pressure and reduce fines generation.
All parts are engineered to withstand the high impact and abrasion typical of cement plant operations, ensuring operational continuity and quality output.
3. Material Selection for Cement Crusher Parts
Proper material selection is key to maximizing crusher wear part performance. We offer a wide range of materials based on your specific operating conditions:
Material | Description | Applications |
---|---|---|
High Manganese Steel | Excellent impact resistance and work hardening properties | Jaw plates, hammers |
High Chrome Alloy | High hardness and wear resistance | Blow bars, impact plates |
Martensitic Steel | Balance of toughness and hardness | Hammer heads, side liners |
Bimetallic Composites | Composite structures for improved performance | Customized parts |
TIC Inserts | Titanium carbide-reinforced steel for extreme wear | Jaw plates, blow bars |
Ceramic Inserts | Advanced ceramic-matrix composites for ultra wear | Impact plates |
Each of these materials can be optimized based on the raw material properties, feed size, moisture content, and desired final product specifications.

4. Customized Solutions for Cement Industry
We offer full customization services tailored to your plant’s unique needs:
OEM/ODM production based on customer drawings and specifications
3D scanning of worn parts for optimized redesign
Logo engraving and part numbering for traceability
Wear pattern analysis for predictive replacement schedules
Alloy selection based on raw material abrasiveness and crusher type
Our R&D engineers collaborate closely with cement plant maintenance teams to design wear parts that improve wear life, reduce downtime, and enhance crushing efficiency.
5. Quality Control and Testing
Our comprehensive quality assurance system guarantees high performance and consistency in every shipment. All crusher wear parts for cement plants undergo:
Chemical composition analysis: to verify raw material quality
Hardness and tensile strength testing: for durability assurance
Dimensional inspection: using CNC and CMM tools
Heat treatment validation: to ensure correct microstructure
Visual and NDT inspections: to detect surface and internal defects
We maintain full traceability of all production batches with quality certificates included in every delivery.
6. Global Applications in Cement Plants
Our cement crusher components are in use at major cement producers worldwide. We support a wide variety of cement plant applications:
Cement kilns in India and Vietnam: primary and secondary crusher parts
Limestone and clay crushing in the Middle East: impact and hammer crusher components
Clinker plants in South America: grate bars, blow bars, and liner plates
Cement recycling facilities in Europe: high-chrome impact solutions
We provide wear parts compatible with leading brands like FLSmidth, Hazemag, Thyssenkrupp, KHD, Sinoma, and more. With a global logistics network, we ensure fast delivery and technical support across continents.
7. Maintenance Tips to Extend Wear Part Life
To maximize the life of crusher wear parts for cement industry, follow these best practices:
Regularly inspect wear patterns for signs of misalignment
Rotate wear parts to use full surface area before replacement
Choose wear materials optimized for specific cement raw materials
Maintain proper feed size and control oversized material
Keep equipment properly lubricated and aligned
We also offer training programs for your maintenance team to improve part handling, inspection, and replacement efficiency.
8. Why Choose Us
✅ Over 15 Years of Wear Parts Manufacturing Experience
✅ Factory Direct Pricing with International Standards
✅ Full Compatibility with OEM Equipment
✅ Custom Design and Engineering Support
✅ Global Shipping and After-Sales Service
✅ Specialist in crusher wear parts for cement industry
✅ In-house R&D and Metallurgical Testing Lab
✅ Fast Quotation Turnaround and Dedicated Technical Support
9. Request a Quote
Looking for a reliable supplier of cement crusher wear parts for cement industry?
📩 Contact us today for pricing, lead time, and technical support.
📧 Email: ljj2914@163.com
📞 WhatsApp: +86-15057942949